Metal Core PCBs
- Home
- Metal Core PCBs
Top Quality Metal Core PCBs
What sets our Metal Core PCBs apart is their unrivaled thermal performance. Engineered with cutting-edge technology, these circuit boards dissipate heat efficiently, ensuring optimal functionality even in high-power applications. These PCBs also include a dielectric layer that ensures proper electrical insulation between the copper layer and the metal core. We understand the critical role of reliability in electronic components. That’s why our Metal Core PCBs are built to last, providing durability that you can trust.
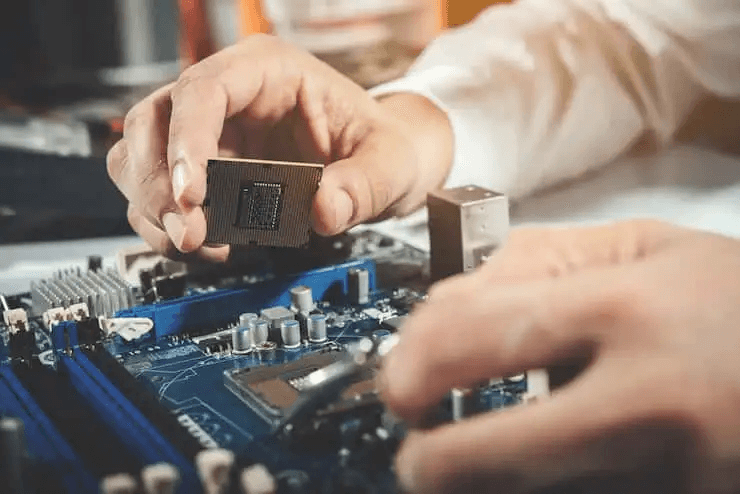
Advantages of Using Our Double-Sided PCBs
Enhanced Thermal Conductivity: Metal Core PCBs, also known as MCPCBs feature a metal core, usually made of aluminum or copper, which significantly improves the thermal conductivity of appliances.
Improved Heat Dissipation: The metal core acts as a heat sink, drawing heat away from critical components. These PCBs prevent overheating and extend the lifespan of electronic devices.
High Mechanical Strength: The metal core provides robust mechanical support to the PCB. This feature makes the MCPCB more durable and resistant to mechanical stresses.
Improved Electrical Performance: The metal cores in these PCBs contribute to better electrical performance by providing a stable and low-impedance grounding plane. It reduces EMI and enhances the signal integrity of electronic devices.
Longer Lifespan: Metal Core PCBs extend the lifespan of electronic devices by efficiently dissipating heat, preventing component stress, and ensuring sustained, reliable performance over time. It reduces the risk of stress-induced failures during temperature fluctuations, making it a safer option for high-power applications.
Real-World Applications:
LED Lighting: These PCBs are extensively used in LED lighting applications. The superior thermal conductivity of the metal core helps dissipate the heat generated by LEDs, ensuring a prolonged lifespan and maintaining optimal performance.
High-Power Supplies: Power supply units, especially those in high-power applications, benefit from MCPCBs. The enhanced thermal management capabilities of metal cores enable efficient heat dissipation, ensuring the reliable operation of power electronics.
Automotive Systems: The Automotive industry uses MCPCBs in various electronic components, such as engine control units (ECUs), LED headlights, and power converters.
Medical Devices: These PCBs are also used in medical devices like patient monitoring systems, imaging equipment, and diagnostic tools, where thermal performance and compact design are critical.
Power Inverters and Converters: MCPCBs play a crucial role in power electronics such as inverters and converters used in renewable energy systems. Their ability to manage heat allows for efficient energy conversion.
Consumer Electronics: Metal-core PCBs are also used in consumer electronic devices, including high-performance audio equipment, gaming consoles, and compact computing devices.

PRODUCTION CAPABILITY | |
Type of Laminates | ACCL – 1W, 2W, 3W |
Aluminium Grade | 6100, 5052, 1060, 1100 |
Laminate Thickness | 0.8 to 3.2 (mm) |
Finish Copper Thickness | Up to 210 microns |
Maximum PCB Size | 1200 mm x 500 mm |
Minimum Track Width | 0.10 mm ( 4 mil ) |
Minimum Track Spacing | 0.10 mm ( 4 mil ) |
Minimum Hole Diameter | 0.60 mm |
Hole/ Outer Profile | CNC Drilling & CNC Routing, Punching & Blanking |
Surface Finishing | ENIG, Gold Plating (Hard Gold), Lead Free HASL, HASL, Lacquer. |
Special Finishes | Carbon Printed Contacts, Peelable Mask. |
Specifications. Standards | IPC-A-600, IPC-SM-840, IPC-RB-276, IPC-TM-650 |
Reports | PDIR, Microsection, Solderability, FAI (First Article Inspection), PPAP Documents (On specific request) |
System Approvals | IATF 16949:2016, ISO 9001:2015, ROHS Compliance |